Step into HARBEC, where CNC mastery meets expertise. Precision is our mantra as we transform your concepts into flawless creations. Whether it’s intricate designs or multi-axis machining, perfection is our commitment. Your Dream, Our CNC Artistry: Embrace HARBEC, where precision knows no limits, and your vision is our compass. Together, let’s craft brilliance.
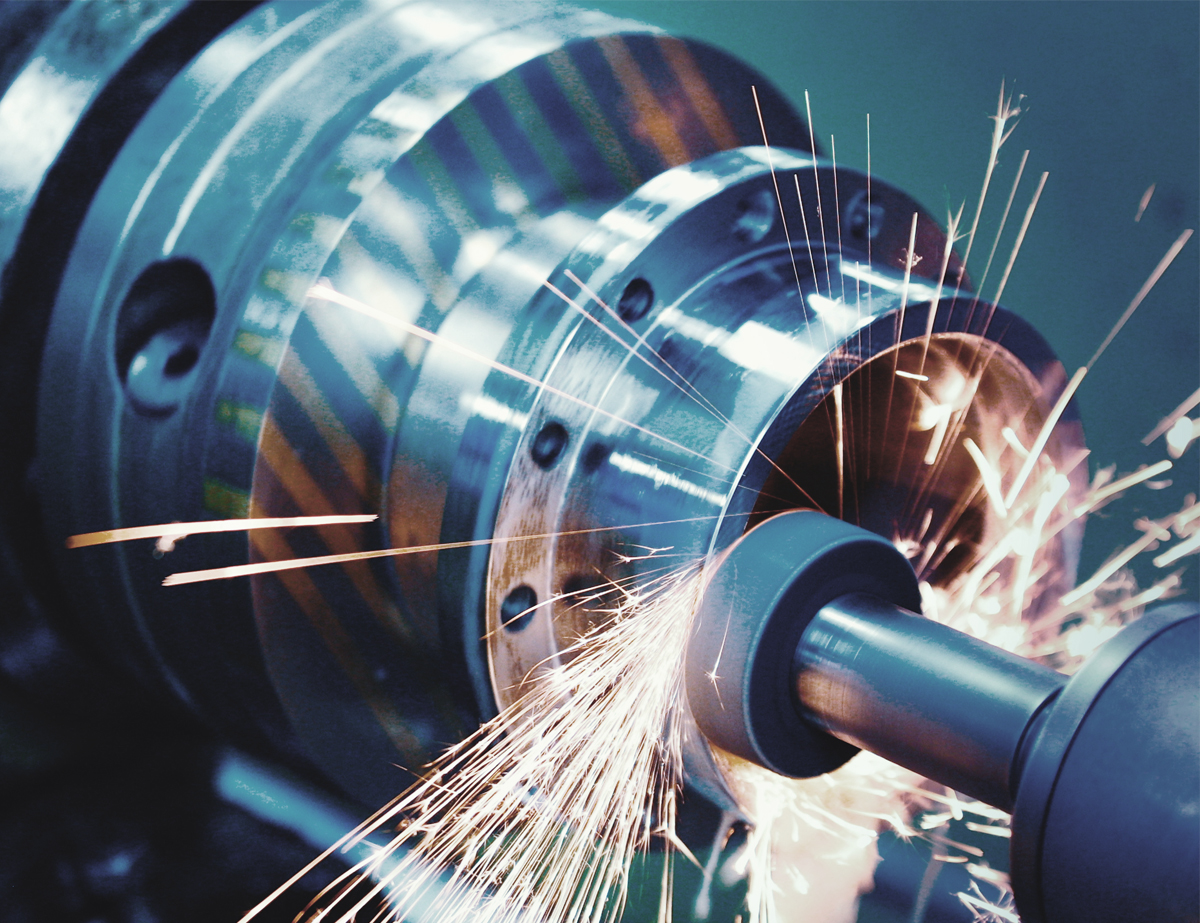
- Design and CAD (Computer-Aided Design): The process begins with creating a detailed 3D model or design of the part using specialized software known as Computer-Aided Design (CAD). This design serves as a blueprint for the CNC machine to follow.
- CAM (Computer-Aided Manufacturing): After the design is completed, CAM software is used to generate the CNC program or code that instructs the CNC machine how to create the part based on the design. This code includes information on tool paths, tool selection, speeds, feeds, and other machining parameters.
- CNC Programming: Skilled operators or programmers create the CNC program by translating the design specifications into a language that the CNC machine can understand. This program guides the machine’s movements and operations.
- Material Preparation: The chosen raw material, such as a metal or plastic block, is securely mounted in the CNC machine’s work holding system.
- CNC Machining Process: The CNC machine follows the programmed instructions to precisely cut and shape the material. The machine’s movements are controlled by motors based on the CNC code, ensuring accuracy and repeatability in the manufacturing process. Various cutting tools, such as drills, mills, lathes, or grinders, are used to remove material and achieve the desired dimensions and surface finishes.
- Quality Control and Monitoring: Throughout the machining process, operators monitor the machine’s operations and may conduct quality checks to ensure the part meets specifications and tolerances.
- Finished Part:Once the machining is complete, the finished part is removed from the CNC machine and may undergo additional finishing processes like deburring, surface treatment, or assembly before it’s ready for use.
CNC machining has many benefits over traditional manual manufacturing techniques. From a single program file, a CNC mill can produce anywhere from one component to several thousand, all of which conform to the exact specifications from the original 3D model. Additional advantages include:
- Efficiency: CNC machines can run continuously with little to no intervention from human operators. This automation drastically increases productivity compared to manual methods, decreasing labor costs and freeing employees to focus on their areas of expertise.
- Consistent Results: CNC machines can replicate their programmed design in any volume, with each iteration adhering to the same dimensions and precise tolerances. With no possibility for human error, CNC machining nearly eliminates variation between components, so it is an ideal choice for high-precision applications.
- Reduced Costs: CNC machining is often the most economical choice for higher volume production runs. The machines can run with less personnel and produce less waste, reducing expenses on multiple levels.
- Flexibility: CNC machines have flexible capabilities in that they can accommodate almost any material and geometry, but they also enable flexible production processes since they can be reprogrammed quickly and with minimal effort.
- Advanced Capabilities: CNC machining enables more intricate designs than could easily be achieved manually. Automated processes like CNC are the best choice for highly complex components, especially those with fine details.
Metal Materials
- Alloy Steels
- Aluminum
- Brass
- Bronze Alloys
- Carbon Steel
- Cobalt
- Copper
- Inconel
- Invar
- Iridium
- Iron
- Kovars
- Magnesium
- Molybdenum
- Monel
- Nickel
- Platinum
- Silver
- Stainless Steel
- Superalloys
- Tin
- Titanium
- Tungsten
- Zinc
Plastic & Non-Metal Materials
- ABS (Acrylonitrile Butadiene Styrene)
- Acetal
- Acrylic
- Composite Materials
- Graphite
- Nylon
- Phenolic
- Polyamide-Imide
- Polycarbonate
- Polyester
- Polyetheretherketone (PEEK)
- Polyetherimide
- Polyethylene
- Polyphenylene Sulfide
- Polypropylene
- Polystyrene
- Polysulphone
- PTFE (PolyTetraFluoroEthylene)
- Teflon
Post-Processing Services
- Anodizing | Titanium | Teflon | Hard Chrome | Sulfuric Acid
- Powder Coatings
- Plating | Zinc | Chromium | Nickel | Electroless Nickel | Cadmium | Copper | Gold
- Dry Film
- Black Oxide
- Passivation | Nitric Acid | Citric Acid
- Shot Peening
- Heat Treating
- Penetrant Inspection
- Non-Destructive Testing
- Pickle and Oiling
- Lubricants
- Polishing | Chrome | Electropolishing | Brushed
- Masking
- Annealing | Complete | Isothermal | Stress Relief
- Primer / Paint Application
- Chemfilm / Chromate Conversion
- Bead Blasting